Supply Chain Planning Software for Process Manufacturers
Proper supply chain management necessitates anticipating demand, limiting risk, and smoothing inventory management to avoid shortages or over-ordering. The right tools can help you improve your supply chain management.
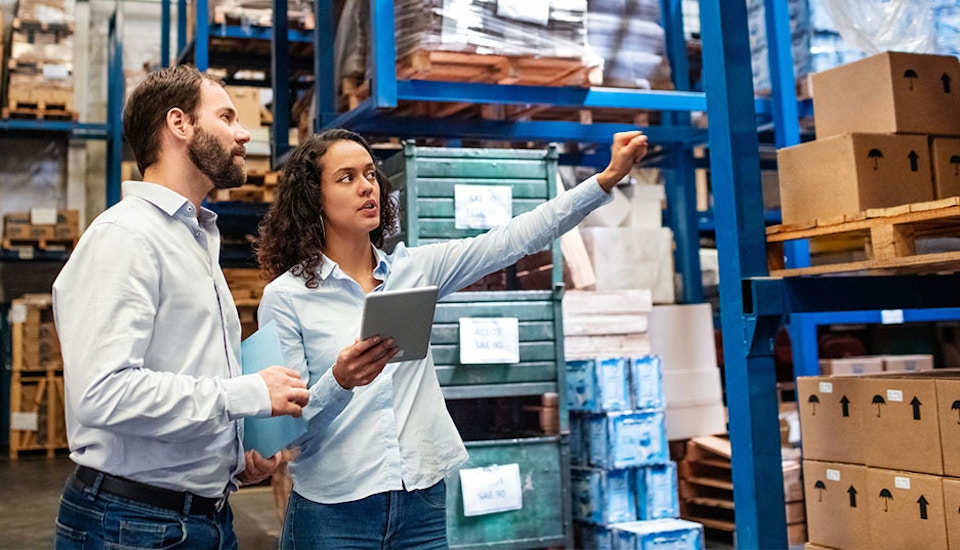
Material Requirements Planning (MRP)
Deacom's MRP software capabilities enable businesses to manage production planning, scheduling, and inventory control within a single ERP system. Users can ensure that raw materials are available for production and that finished goods are ready for delivery with MRP functions, including waste reduction, manufacturing activity planning, and delivery schedule management. Deacom's MRP system calculates demand based on scheduled sales orders, scheduled production jobs, and indirect requirements. Indirect requirements refer to the quantity of materials needed to fulfill suggestions for a displayed item in the Bill of Materials.
Native MRP Functionality
Deacom’s MRP system is one of the most important tools from a production planning perspective. In this quick demonstration of the software, we show how you can use the MRP report to view what items are in planning and how to create a new production job.
Deacom gives you production capacity planning software features to meet your complex manufacturing requirements
Production Capacity Planning
Determine your business’ future equipment utilization rates based on sales or production forecasts.
- Gain insight into labor requirements necessary to support your production plans
- Run multiple forecast scenarios to understand the impact of situations on production capacity
- Plan by day, week, or month based on your business’s operational structure
- Forecast at the finished good level and ensure that capacity exists for bulk production as well
- Answer questions related to supporting existing business, fitting new orders, and future investments
Production Management
Create, schedule, stage, and analyze production jobs more easily.
- Plan production quantity within a defined timeframe with materials and labor
- Choose from three calendars: Jobs, Jobs Inventory, or Master Production Calendar
- Use substitute materials if necessary to complete production jobs
- Finish inventory using various methods and system areas
- Assign catch weights and serial numbers for proper tracking and production accuracy
- Filter and sort data with selection criteria for detailed analysis and order grouping
- Enforce security for finishing and closing jobs
- Understand how inventory and ledger are impacted when issuing inventory
Production Line Scheduling
Control and improve your production schedule based on work routing sequences.
- Drive Just-in-Time (JIT) production and minimize production downtime
- Improve visibility to maintenance activities and create a single view of production activities
- Schedule routings based on established sequencing rules to minimize downtime or maintenance activities
- Trigger jobs to be scheduled based on the earliest or latest production availability
- Build maintenance tasks into the production schedule.
- Shift the production schedule based on actual machine output and evaluate scheduling options with What-If scenarios
- Manually schedule or shift routings around on the calendar and shift linked routings in sequence during manual moves
- Gain insight into production efficiency through robust reporting
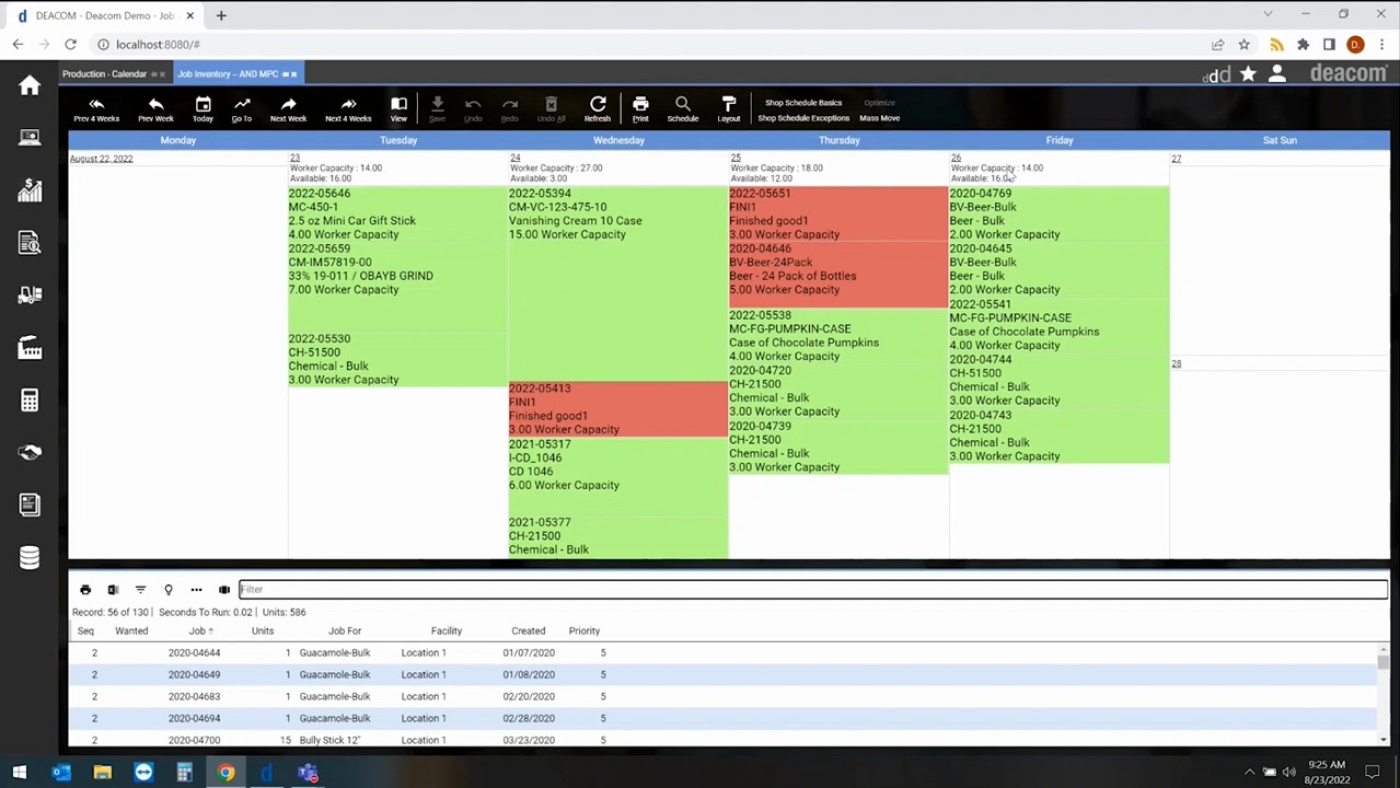
See Deacom's Production Scheduling Capabilities in Action
Built-in scheduling capabilities in the Deacom ERP system allow you to determine what will be produced on which days, including any form of capacity calculation you wish to employ to establish if you'll be within that day's capacity.
Product Lifecycle Management (PLM)
Deacom software is designed to handle PLM for your batch and process manufacturing company. It is a comprehensive ERP platform tailored to the needs of your small to medium-sized business within industries such as Food & Beverage, Chemical and Coatings, Cosmetics, Pharmaceuticals, and Nutraceuticals, among others. Deacom includes the necessary business management capabilities that meet your complex needs as process manufacturers, going beyond the basic functionality offered by traditional ERP solutions.
This unique software can help your business simplify the process of developing, creating, and manufacturing new products and formulas. Deacom ERP software provides formulation management capabilities, allowing you to add and maintain bills of material, revisions, and associated costs, configure overage and degradation factors, and define batch yields. Deacom then provides a solution for creating, scheduling, staging, and analyzing production jobs that are tied to these. It can also help eliminate manual processes and manage all manufacturing operations from one centralized location.
Dock Scheduling
Improve operational efficiency at the dock by managing a real-time dock calendar and prevent loads from being missed while making sure labor resources are available. Dock scheduling features include:
- Drag and drop loads
- Minute-by-minute scheduling
- Unit of measure default loading times
- 3PL integration
- Automatic appointment triggers
- Management of inter-company transfers
Sales Forecasting
Utilize sales predictions in strategic planning to guide purchase and manufacturing activities, enabling informed, data-driven demand planning decisions.
- Plan forecasts by day, week, or month based on business requirements
- Plan demand around facility hours and holidays with forecast blackouts
- Update sales forecasts based on upcoming product promotions using the promotional lift
- Establish frozen, slushy, and liquid forecast zones for planning activities with forecast zones
- Utilize forward or backward consumption strategies to account for actual sales with forecast consumption
- Build accounting forecasts and budgets based on sales forecasts with revenue projections
- Plan production resources based on a sales forecast
- Provide an audit trail for all changes made to a forecast with historical tracking
- Import forecasts from Excel, Access, or other structured data formats
FAQs
Can the software help minimize inventory handling costs?
Yes, the Deacom ERP solution can help minimize inventory handling costs with features such as material requirements planning (MRP) and inventory management. These capabilities allow businesses to optimize their inventory levels, streamline procurement processes, and avoid stockouts or excess inventory. By having better visibility into inventory levels and demand, manufacturers can reduce carrying costs and improve cost-efficiency in their supply chain operations.
How does the software maximize production output?
Deacom offers production planning and scheduling functionalities that enable businesses to optimize their production processes and maximize output. It provides tools for capacity planning, production scheduling, and resource management, allowing batch and process manufacturers to effectively allocate resources, minimize downtime, and improve overall production efficiency. By streamlining production workflows and ensuring timely availability of materials, the software helps businesses achieve higher production output.
Is the Deacom ERP solution configurable to fit the unique needs of every manufacturing business?
Deacom is built from the ground up to meet the complex requirements of batch and process manufacturers. But it is also configurable to fit the unique needs of these different manufacturing businesses. It can accommodate industry-specific requirements, process variations, and specific workflows, ensuring a personalized fit for each business's operational needs.
Are there any specific industries or sectors that can benefit from this software?
While the Deacom ERP solution provides core functionalities that are applicable across manufacturing industries, it has particularly strong capabilities in process manufacturing industries such as food and beverage, chemicals, pharmaceuticals, cosmetics, and other regulated industries. The software's ability to handle batch production, formula management, regulatory compliance, and quality control makes it well-suited for these industries.
Is the software scalable to accommodate business growth?
Yes, the Deacom ERP software is designed with scalability in mind. It can handle the needs of both small and mid-sized enterprises and is capable of handling increased transaction volumes, user counts, and multi-site operations, ensuring the scalability to support your business growth.
How does the software optimize supply chain operations and improve overall efficiency?
The ERP software optimizes your operations and improves overall efficiency through various features and functionalities. It provides end-to-end visibility into business processes and supply chain transactions, enabling better decision-making and real-time monitoring of operations. The software automates manual tasks, provides efficient inventory planning, streamlines workflows, and eliminates data silos, reducing errors and improving operational efficiency. With native capabilities for inventory management, production planning, procurement, sales, and financials, the software facilitates seamless data flow and process integration, leading to improved efficiency and productivity across the organization.
Take the leap and transform your supply chain today.
Experience the power of Deacom ERP on your supply chain operations.